The paper factory Palm GmbH & Co. KG, based in Aalen (Baden-Württemberg) in Germany, says it plans to produce corrugated base paper from wastepaper in an extremely energy-efficient and high-quality manner.
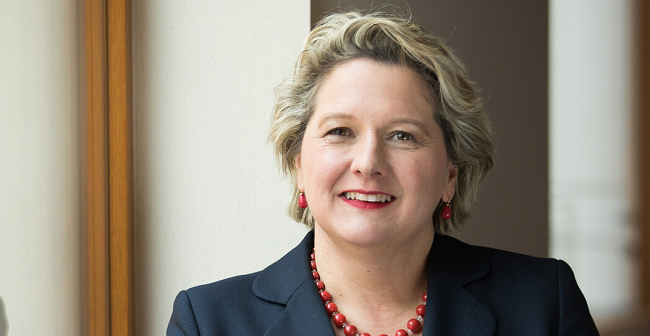
Compared to conventional technology, energy consumption is reduced by 27 percent with a new technology. The pilot project is funded with over €770,000 from the environmental innovation programme.
Corrugated base paper, which is the starting product for packaging, is made from 100 percent different types of wastepaper in a constantly optimized recycling process. It happens that valuable recyclable fibers are sorted out together with the contaminants present in the wastepaper and are lost to the process. It therefore makes sense to adapt the pulping units to the respective strength properties of the wastepaper used.
This is to be implemented at the Palm paper mill with a new type of defibering technology for wastepaper. The aim of the innovative project is to increase the fibre yield to almost 100 percent while using less energy. The technical solution behind the optimised recycling process is the “Green Pulping Concept”, which combines two pulping technologies.
With an annual production volume of 750,000 tons of corrugated board base paper, the family company can save 7,440 megawatt hours of energy and, as a result, reduce CO2 emissions by 2,403 tons. Due to the high strength of the processed paper, fewer chemical additives are used, and the circulation water is relieved.
The innovative technology can in principle also be transferred to other paper mills, so that a multiplier effect is possible for the entire industry. The environmental innovation programme promotes the first large-scale application of an innovative technology. The project will go beyond the state of the art and have a demonstration character.